今回の記事では、プリント基板製造の流れについて詳しく解説します。
最後に、基板製造での課題解決事例もご紹介します!
基板製造の基礎知識を知りたい方に是非読んでいただきたい記事です!
プリント基板製造の流れを理解しておくことで、基板の種類に応じた工程を選択できます。
当記事では、プリント基板の基本的な製造の流れをご紹介いたします。
2層プリント基板製造の基本工程
プリント基板製造の大まかな流れは以下のようになります。
1.ガーバーデータの作成
2.フィルムの作成
3.基板穴の作成
4.銅メッキとパターンの形成
5.ソルダーレジストの形成
6.表面処理
7.シルク印刷
8.外形加工
9.検査
上記の流れを詳しく解説します。
1.ガーバーデータの作成
基板設計を終えたCADデータから基板製造用のデータを出力する必要があります。このデータをガーバーデータと呼びます。併せて穴データなどの製造用の各種データ一式を出力します。
2.フィルムの作成
ガーバーデータから基板製造用の各種フィルムを作成します。
3. 基板穴の作成
NCデータをもとに基板上のスルーホール用の穴をあけます。一般的には、ドリル加工で行いますが、最近は基板の微細化に伴いビルドアップ基板ではレーザー加工で対応することもあります。基板の穴あけはプリント基板の加工で最も時間がかかり、穴数でコストも変動します。穴のサイズを大きくすることや、穴の数を減らすことで加工費の削減が可能です。
4.銅メッキとパターンの形成
表面と裏面の銅箔面を電気的に接続するために、銅メッキによってビア形成を行います。ドライフィルムを貼付します。その後、ドライフィルムの上から感光性のあるレジスト剤を塗り、露光・硬化させた後、薬剤で銅メッキを取り除きます。すると、レジストを塗った箇所の銅メッキだけが残り、基板上にパターンが形成されます。最後に、ドライフィルムを基板から剥がします。多層基板の場合、作成した基盤の上から絶縁層を圧着して同様の工程を再度行います。
5.ソルダーレジストの形成
パターンが基板上で露出していると、絶縁被膜がないため、銅箔同士がショートする、表面に金属片やはんだが付いてショートする、といった問題が生じてしまいます。不良を起こさないよう、絶縁被膜のソルダーレジストを基板表面に塗り、パターンを保護します。工程4のパターン形成で使用したレジストとは違い、ソルダーレジストは、基板製造完了後も基板に残り、基板を保護します。
6.表面処理
一例としては、パターン露出部に半田付け性の向上や銅箔部の防錆を目的に基板にはんだメッキをします(有鉛と無鉛があります)。高温状態のはんだ槽に基板を投入し、高温・高圧の熱風を吹き付け、はんだを基板に均一に塗ります。レジスト層には、はんだが塗布されないので、部品実装部分にのみはんだを塗布することができます。はんだメッキ以外では無電解金メッキ(金フラッシュ)をすることもあります。フラックス処理の場合はフラックスを塗布することになります。
7.シルク印刷
プリント基板への部品実装時にガイドの役割をするシンボルマークやロゴなど機能性を高めるため、視認性をよくするためにシルク印刷をします。
8.外形加工
シルク印刷まで終わると最終製品の外形サイズにあわせてルーターで外形加工をしたり開口部の加工をします。
9.検査
プリント基板を製造した後は基板に不具合がないかどうかを検査します。導通部分にテストピンを当てて、回路のオープンショートをチェックする工程(導通検査)、目視や画像認識カメラを使ってチェックする工程の2工程があります。
上記のような流れでプリント基板は製造されます。
プリント基板製造での課題解決事例をご紹介!
アナログ回路・基板 設計製作.comで行った基板製造での課題解決事例をご紹介します。
課題解決事例① バックドリル加工によりテスト基板製造コストを削減
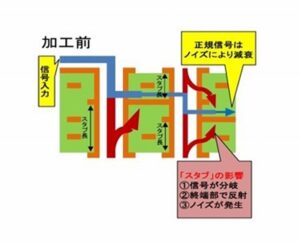
医療機器用の映像処理用基板では、高電圧基板が用いられることが多くあります。当事例のお客様は、高電圧用の試作基板を製造し放電のテストを行いたいとのご要望をお持ちでした。
従来、隣り合うスルーホールの電位差による放電確認では、都度ビルドアップ基板を作成し、条件を変更することでテストを行っていました。しかし、ビルドアップ基板を製造するにはコストがかかり、試作段階の費用を低減したいとのご意向でした。
そこで当社は…
>>詳細はこちらから!
課題解決事例② フットプリント形状変更で反りの発生を回避
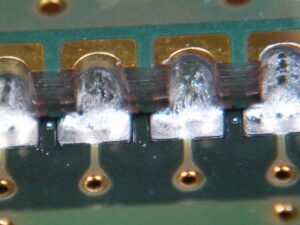
通信機器に搭載される情報通信用基板について、2枚の基板を重ねスルーホールで接続する仕様でした。上の基板には通信モジュールを使用しています。
親基板と子基板の2枚の基板を重ねる場合、基板が反ることにより基板同士が密着せず半田付けにむらが出ることにより、通信不良が発生するリスクがあります。当事例では、基板が薄く、基板製造時にそりが発生しやすくなっていました。そりの発生により、スルーホールのうえまで半田が上がりきらず、通信モジュールが動かないというトラブルにつながっており、改善が必要でした。
そりの発生による通信不良発生リスクを回避するため、基板設計から基板製造、基板実装まで一貫して対応でき、ノウハウを持つ当社にお声かけ頂きました。
まず、そりの原因を調査したところ、従来は6面付け/1シートの仕様であり、そりが発生しやすいことが判明しました。そこで…
>>詳細はこちらから!
課題解決事例③ ファインピッチと大電流対策の実現
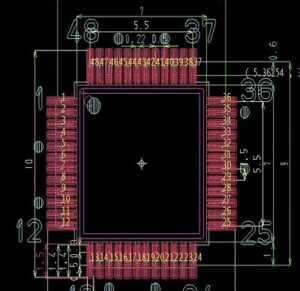
通信機器用の電源基板において、大電流対策のため厚銅基板(70㎛)が使用されていました。大電流の場合、銅箔厚を厚くするのが必須ですが、今回、ファインピッチで部品を実装する必要がありました。ファインピッチの場合、銅箔厚を薄くする必要があります。銅箔厚が厚いとオーバーエッチングのため、細いパターンが断線する恐れがあるためです。
大電流対策のため銅箔厚を厚くする必要がある一方で、ファインピッチ対応のため銅箔厚を薄くしなければならないというジレンマに対応できるメーカーがなく、当社にお声かけ頂きました。
大電流となるため、銅箔厚は落とせませんでしたが、35㎛の銅箔に銅メッキで厚付けをして70㎛にすることで、ファインピッチに対応しました。
また、基板製造時…
>>詳細はこちらから!
プリント基板の製造まで当社にお任せください!
いかがでしたでしょうか。
プリント基板の製造の工程についてご理解頂けましたでしょうか。
アナログ回路・基板実装製作.comを運営するシスプロは、アナログ回路・基板の製造まで一貫して行います。
アナログ回路・基板の製造にお困りの皆様、お気軽に当社にご相談くださいませ!
>>お問合せはこちら!
アナログ回路・基板 設計入門の無料冊子をDL!
アナログ回路・基板 設計製作.comでは、技術資料を無料で発行しております。是非ご確認ください。
以下は、電源基板やRF基板を設計するうえで必須となるアナログ回路・基板の設計に関するポイントをまとめた無料冊子です。
高電圧や大電流の電源基板、高周波のRF基板など、アナログ回路・基板の設計は複雑で難易度が高いものとされています。
ベテラン設計者の方には知識の棚卸としてご活用いただき、新任設計者の方の教育資料としてもご活用ください。
入門書としてこの一冊を活用頂き、皆様の設計活動の一助になれば幸いです。
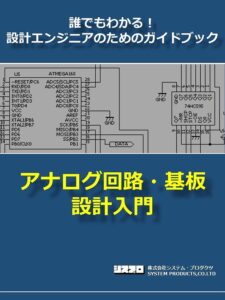
>>お役立ち資料はこちらから無料DL!